In modern manufacturing, CNC machining centers are key equipment, and their performance directly affects production efficiency and product quality. As the core control part of CNC machining centers, the reliability and stability of internal electrical connections in electrical cabinets are crucial. WAGO TOPJOB® S rail-mounted terminal blocks play an indispensable role in CNC machining center electrical cabinets with their advanced technology and excellent performance.
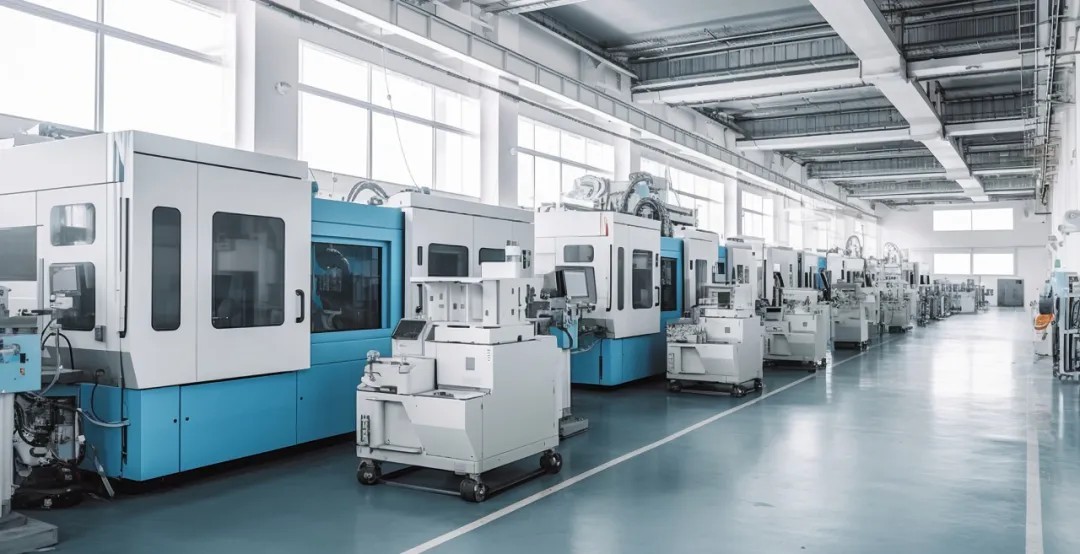
Challenges of CNC machining center electrical cabinets
During the operation of CNC machining centers, electrical cabinets face many challenges. There are many internal electrical components and complex wiring, and efficient connection solutions are required to ensure the accuracy and stability of signal transmission; at the same time, vibration, impact and electromagnetic interference may be generated during the operation of the machining center, which requires the terminal blocks to have good vibration resistance, impact resistance and anti-interference ability to ensure the reliability of electrical connections. In addition, with the continuous development of CNC technology, the requirements for miniaturization and intelligence of electrical cabinets are getting higher and higher, and traditional wiring methods are difficult to meet these needs.
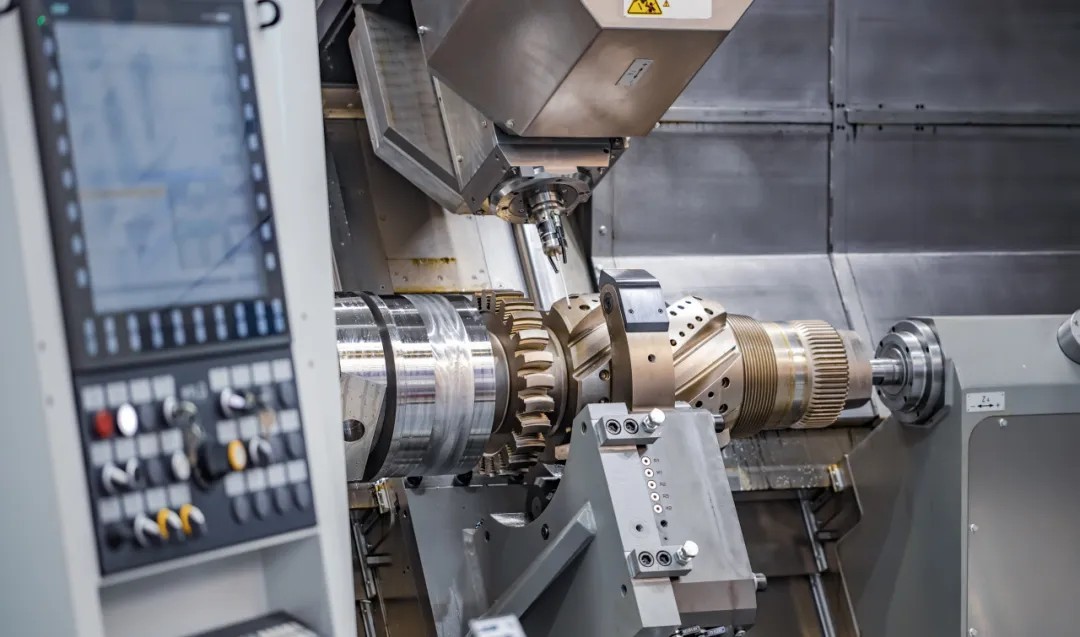
Advantages of WAGO TOPJOB® S rail-mounted terminal blocks
01 Reliable and stable connection
WAGO TOPJOB® S rail-mounted terminal blocks use spring clamping connection technology, which uses the elastic force of the spring to firmly clamp the wire in the terminal. During the operation of the CNC machining center, the wire will not fall off even if it is subjected to strong vibration and impact.
For example, in some high-speed cutting CNC machining centers, the machine tools will generate large vibrations during operation. After switching to WAGO rail-mounted terminal blocks, the reliability of the electrical system has been significantly improved, and the number of shutdowns for maintenance has been significantly reduced.
02 Easy installation and maintenance
The staff only needs to insert the wire directly into the terminal to complete the connection, without the use of additional tools, which greatly saves wiring time. During the installation and commissioning of the electrical cabinet of the CNC machining center, this feature can significantly improve work efficiency, reduce maintenance costs and downtime.
For example, when replacing a sensor in the electrical cabinet, using WAGO TOPJOB® S rail-mounted terminal blocks, the staff can quickly remove and reconnect the wires, so that the equipment can resume operation as soon as possible.
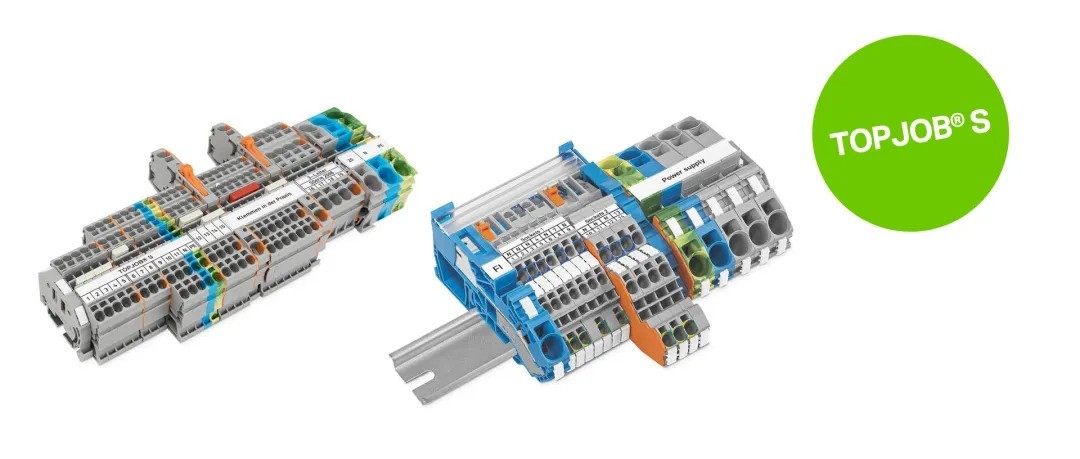
03 Compact design saves space
The compact design allows more connection points to be achieved in a limited space. This is especially important for CNC machining center electrical cabinets with limited space, as it can help achieve a more compact and reasonable wiring layout and improve the space utilization of the electrical cabinet. At the same time, the compact design is also conducive to heat dissipation and reduces the risk of damage to electrical components due to overheating.
For example, in some small CNC machining centers, the electrical cabinet space is small, and the compact design of WAGO TOPJOB® S rail-mounted terminal blocks makes wiring more convenient and also improves the stability of the electrical system.
WAGO TOPJOB® S rail-mounted terminal blocks provide efficient and stable electrical connection solutions for CNC machining center electrical cabinets with their advantages such as reliable connection, convenient installation and maintenance, adaptability to complex environments, and compact design. As CNC machining technology continues to develop, WAGO rail-mounted terminal blocks will continue to play an important role in helping the manufacturing industry achieve a higher level of automation and intelligent production.
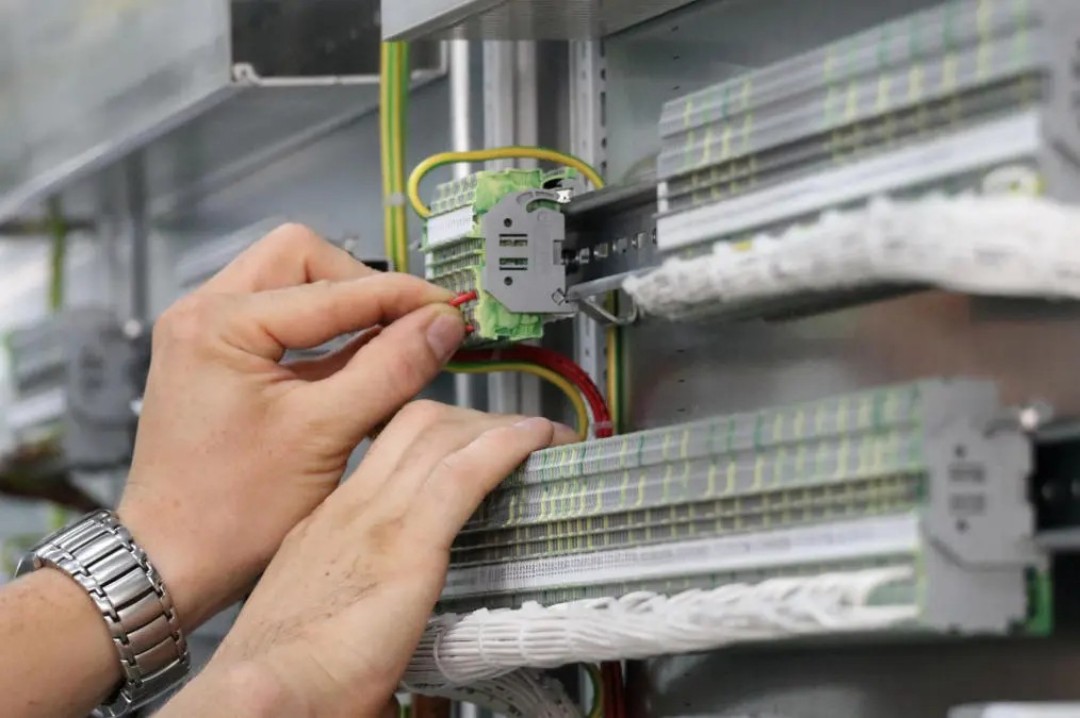
Post time: Mar-14-2025